Improving the hardness of high chrome grinding balls requires a comprehensive approach involving material composition design, heat treatment process optimization, microstructure control, and surface treatment technologies.
Optimizing Alloy Composition
The hardness of high chrome grinding balls is closely related to their alloy composition, particularly the chromium content.
By increasing the chromium content, the hardness of the cast balls can be significantly enhanced. Typically, chromium content ranges between 15%–30%, with higher percentages yielding greater hardness. Additionally, adding appropriate amounts of alloying elements such as molybdenum, vanadium, and tungsten can further improve hardness and wear resistance. The effectiveness of each alloying element varies, so their ratios must be tailored to specific operating conditions.
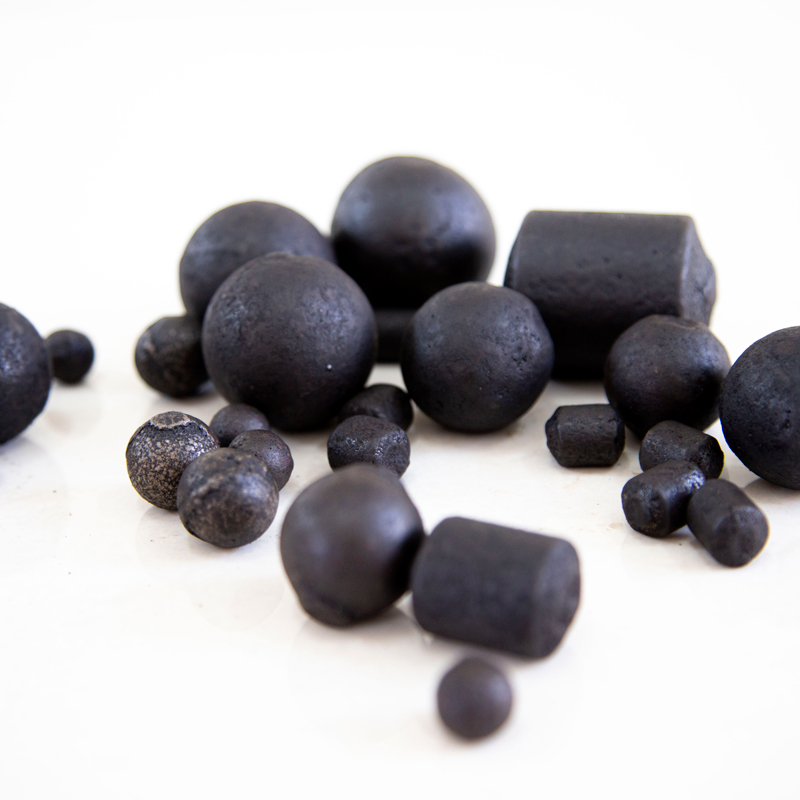
Schleifkugellieferanten
Controlling Casting Processes
The cooling rate of molten metal during casting has a significant impact on final hardness.
Rapid cooling techniques can refine the grain structure during solidification, thereby increasing hardness. Fast cooling not only enhances hardness and wear resistance but also reduces casting defects.
Heat Treatment Processes
Heat treatment plays a critical role in improving the hardness of high chrome grinding balls. Processes such as quenching and tempering can significantly enhance hardness and optimize microstructure.
Common heat treatment methods include:
Quenching: Heating the balls to a specific temperature followed by rapid cooling to form a martensitic structure, which boosts hardness.
Tempering: Post-quenching tempering reduces internal stresses and balances hardness, toughness, and wear resistance.
Refining Grain Structure
High hardness high chrome grinding balls are affected by grain size. The smaller the grain, the higher the hardness. By optimizing the alloy composition, casting parameters and cooling rate, the grain structure can be refined to obtain excellent hardness.
Improving Spheroidization Process
Spheroidization is a key step in manufacturing high chrome grinding balls. Proper spheroidization can form a high-hardness alloy layer on the surface, enhancing both hardness and wear resistance. This process can be optimized by adjusting melting temperatures, mold design, and cooling methods.
Controlling Microstructure
Through precise alloy additions and cooling control, the microstructure of high chrome grinding balls can be optimized.
Common structures include martensite and bainite. Martensite typically offers higher hardness compared to other phases. By adjusting cooling rates and alloy composition, a stable martensitic structure can be formed to maximize hardness.
Advanced Detection and Control Technologies
Modern online monitoring technologies, such as X-ray diffraction analysis and scanning electron microscopy (SEM), enable precise real-time control of hardness and microstructure. These tools ensure product consistency and quality.
Surface Strengthening Techniques
Surface treatments like laser hardening or electroplating can further enhance surface hardness and wear resistance. These techniques extend service life by improving surface properties without altering the core material.
The core strategy for improving the hardness of high chrome grinding media balls lies in coordinated optimization of alloy design, casting processes, heat treatment, and surface strengthening. By rationally balancing alloy elements, refining casting parameters, and optimizing heat treatment, the hardness and wear resistance of grinding balls can be significantly enhanced. This extends service life and reduces grinding costs in industrial applications.